新しいナノパターニング(テクスチャリング)技術
新しいナノスケールの表面パターニング技術である「ナノストライプ構造」を開発しました。ナノストライプ構造の作製には、MEMS製造技術が用いられています(図1)。最初に基板上にマイクロスケールの周期的な傾斜構造を作製します。次に、物理蒸着法(PVD)によって多層膜を形成します。最後に、基板表面を研磨すると、多層膜の材料が表面に縞状に現れます。マイクロスケールの構造を異方性エッチングで形成すると、Siウェーハ全体に周期的な傾斜構造が得られます。また、機械加工を使用して周期的傾斜構造を形成する場合、周期を細かくするほど加工時間は長くなりますが、金属を含むさまざまな材料に適用することができます。
研磨条件や多層膜の材料の組み合わせによっては、研磨時に一方の材料が他方よりも低く削られ、研磨面全体にわたってナノスケールの凹凸構造が得られます(図2)。このとき得られる凹凸の総数は、マイクロスケール傾斜構造の数と多層膜の膜数の積に比例するため、加工効率が飛躍的に向上します。また、多層膜の厚さを薄くしていくと、数十nmまたはそれ以下のパターンピッチも可能です。本手法は、材料の選択性が広く、加工プロセス全体での優位性が多岐にわたります。
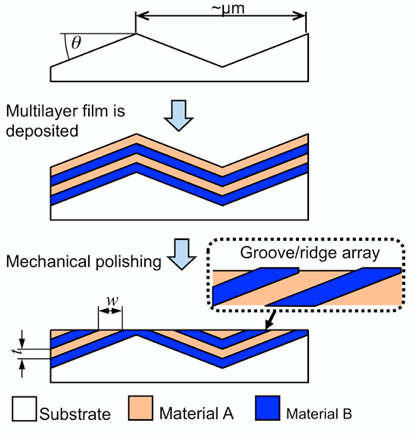
図1 ナノストライプ構造の概要。ミクロンスケールの周期的な傾斜構造を作製し、その上に多層膜を蒸着。研磨をすると多層膜の断面が表面に露出してナノストライプ表面となる。
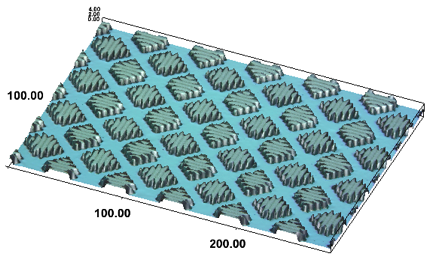
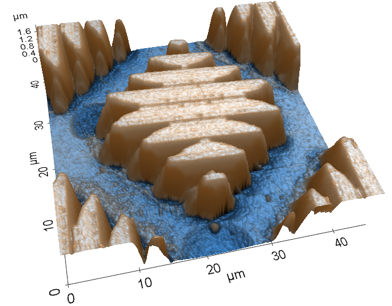
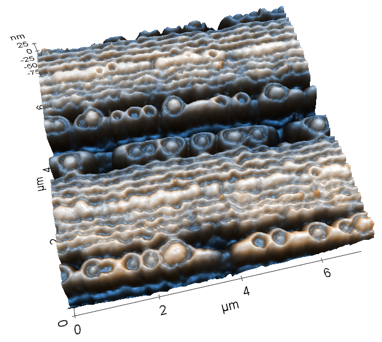
図2 ナノストライプ構造の例。1層の厚さが50nmのCとSiCを交互に30層ずつ積層し、研磨したときに得られた表面のレーザー顕微鏡像(左)とAFM像(中、右)
マイクロナノパターンの潤滑特性
ナノストライプ構造を正面から見たとき、パターンの配置(2次元パターン)が異なる4種類の試験片を用意した.直線の溝を断続的に配置したパターン(タイプⅠ) (Fig.1(a)),及び摺動方向に対してV字型の溝を連続的に配置したパターンを用意した.V字型のパターンは隣り合うV字の溝同士を連結させたタイプⅡ(Fig.1(b)),隣り合うV字同士の間隔を空け,V字を隔てる領域が対向面に接触するタイプⅢ(Fig.3(c))と隔てる部分を溝にしたタイプⅣ(Fig.3(d))の4種類である.
速度を変化させて摩擦速度と摩擦係数の関係を調べると、混合潤滑から流体潤滑領域の摩擦特性を示した。次に、ナノ溝の効果を検討する為に,まず各試験のナノ溝の面積率を調べた.ナノ溝の面積率は,レーザー顕微鏡を用いて表面を測定し,輝度の違い及び溝の深さの明暗を解析することで算出した.図2にナノスケールの溝の面積率と低速域の摩擦係数の関係を示す。ナノスケールの溝の面積率が高いほど摩擦係数が低い傾向が示された。
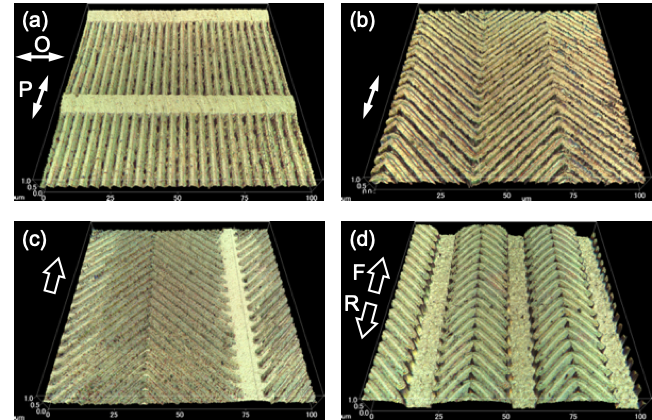
図1 摩擦実験に用いたナノストライプ構造のレーザ顕微鏡画像。摩擦方向は矢印で図中に示している。(a)は直線状のパターンのType I、(b)はType II、(c)はのType III、(d)はのType IVである。(c)から(d)はV溝から構成されている。(c)はV溝のの境界が高く、(d)はV溝の境界が低くなっている。(d)では、R方向よりもF方向に摩擦したときに摩擦係数が低くなった。
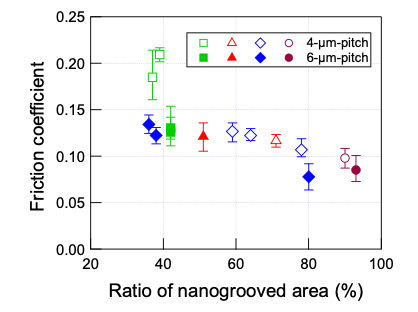
図2 境界潤滑領域におけるナノ溝の面積率と摩擦係数の関係。四角 (□, ■), 三角 (△, ▲), 菱形 (◇, ◆), 及び丸 (○, ●) のプロットは、それぞれType I, Type II, Type III, Type IVのパターン配置を表している。ナノスケールの溝パターンが広く接触しているほと、低速では摩擦係数が低くなることが示された。
【ナノパターンの自己再生】摩擦試験後にAFMで観察した表面形状を図3に示す。全体に平滑化されており、摩耗が進展している様子が示されている。ナノスケールの溝に着目すると、20nm程度の深さを維持している。2種類の材料(CuとAg)の摩耗率の差と潤滑油中に含まれている添加剤の腐食効果により、摩耗してもナノパターンが維持されていると考えられる。
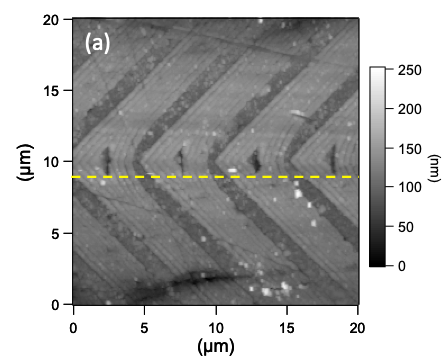
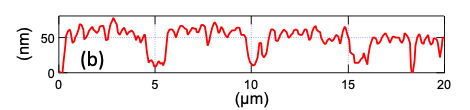
図3 摩擦後に観察されたナノストライプ構造試験片のAFM像。(a)では全体的に摩耗によって平滑化している。点線部分の断面図(b)では、20nm程度の溝が認められる。
ここがポイント!
平面同士を潤滑条件下で摩擦させるために回転型摩擦試験機を用いています。その際に、ナノストライプ面で3つのパッドを構成し、平滑なSIC単結晶ディスクに押し当てることで、均一な接触を実現します。
マイクロナノパターンの組合わせによる摩擦係数制御
周期的な表面パターンの組み合わせによる摩擦特性を明確にするために、曲率半径が150 mmの円筒表面に作られたナノストライプ表面を用いて、0.7 µm/s から 0.7 mm/s のスライディング速度で摩擦試験が行われました。ナノストライプ表面には、マイクログルーブが6 µmのピッチで配置され、2つのマイクログルーブ間のリッジ部には約500 µmのピッチでナノグルーブが形成されています。ナノストライプ表面を滑らかなシリコン表面に擦り付け、滑り方向がグルーブと平行な場合、特に3.4 µm/s未満の低速度では、最低の摩擦係数0.1が測定されました。2つのナノストライプ表面の組み合わせでは、両表面のストライプの溝が滑り方向に垂直な構成および両表面のストライプの溝が互いに直交している構成において、最大の摩擦係数が測定されました。前者の構成では、マイクログルーブの傾斜によって生じる付着力が測定された摩擦力で優勢でした。
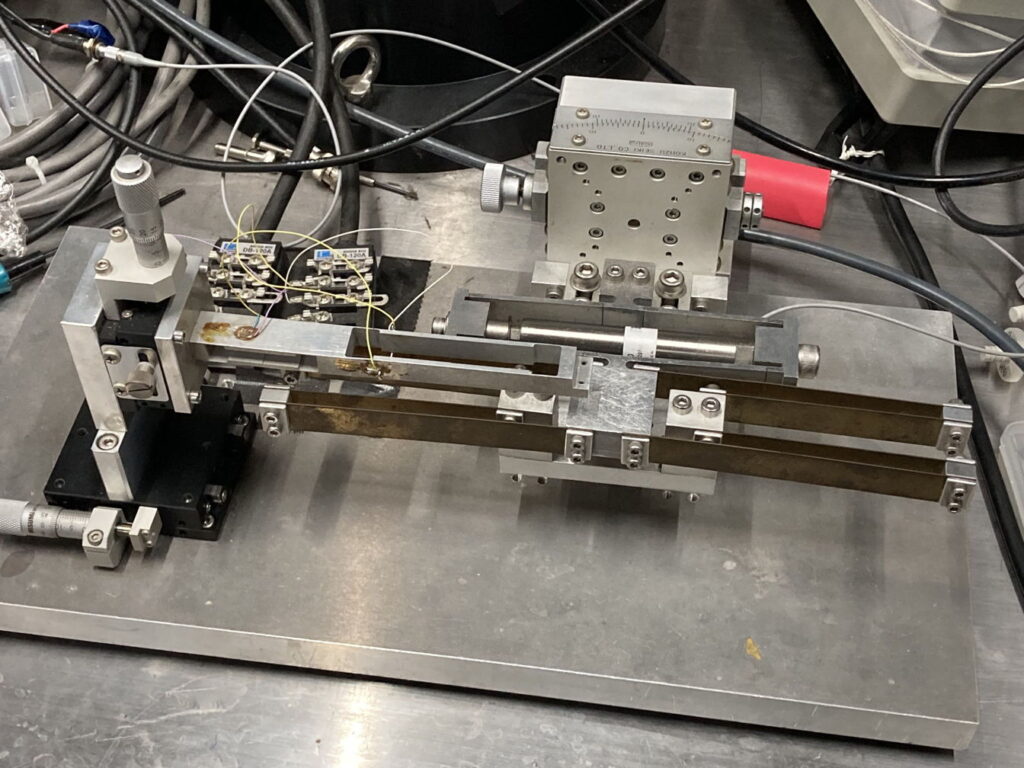
図1 実験に用いた低速摺動摩擦試験機。駆動にPZTアクチュエータを測定時のノイズ発生を抑えながら、超低速摺動が可能になる。また、摩擦面を組合わせた時の相対的な角度を変えることも可能。
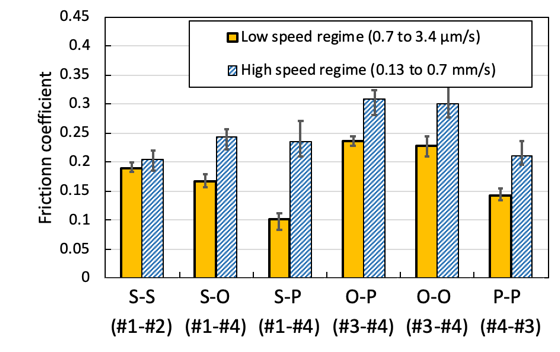
図2 向かい合う面に形成された溝の摩擦方向に対する角度によって多様な摩擦係数が実現できる。O、Pはそれぞれ摩擦方向に対して直交、平行の溝を表す。Sは平滑な面。最小の摩擦係数は平滑面(S)に対して平行な溝(P)を滑らせた時に得られる。最大の摩擦係数は、摩擦方向に対して直交する溝(O)の組合わせで得られ、摩擦速度に対して一定の摩擦係数が実現できる(図3に説明)。
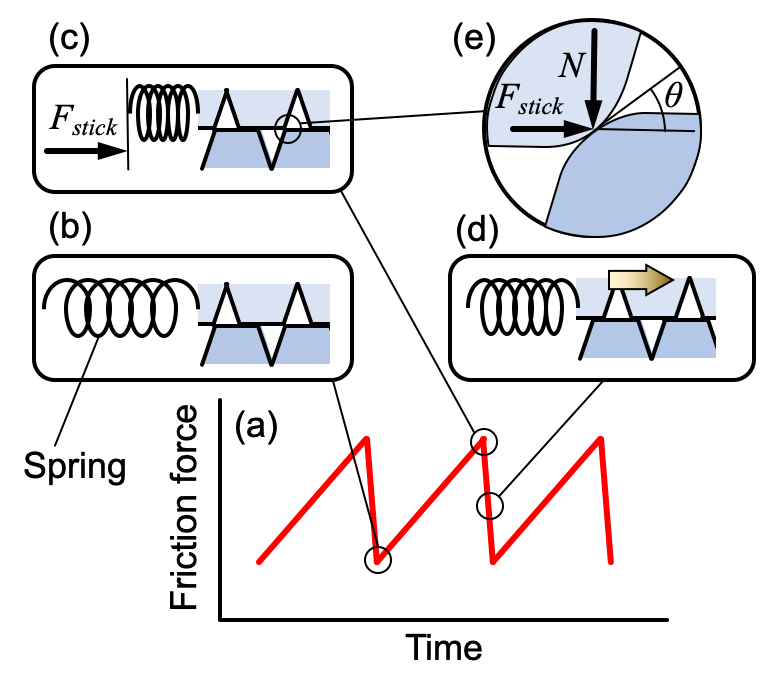
図3 溝同士が咬み合う条件でのるスティックスリップによる摩擦力と接触幾何学との関係。 (a) 摩擦力は周期的に変動する。 (b) マイクロスケールの山は対向する山にスティックしている。押し付け力は (b) から (c) にかけて増加し、(c) で最大となる。その後 (e) で滑りが発生。 (c) での作用する力は (d) に示されていいる。
ここがポイント!
図3の構造で一定の摩擦係数を実現するためには、スリップ時の摩擦係数を低く抑える必要があります。山の頂上には実際にはナノ溝配列が形成されており、それにより低摩擦と低摩耗が実現し、安定した摩擦係数が得られました。
真空環境下での固体潤滑に関する研究
高温環境や真空環境では,油などの流体による潤滑が困難なため,固体潤滑により摩擦の低減が図られることがあります。固体潤滑の問題の一つは、潤滑膜が摩耗したりはく離したりすると,補修が出来ないことが問題点として挙げられます。軟質金属と硬質金属を組み合わせからなるナノストライプ構造を固体潤滑表面として用いると、摩耗により軟質金属が硬質金属上を覆い,「硬質材料が荷重を支え軟質材料がせん断抵抗を受け持つ」という低摩擦の条件が実現できます.これまでに、CrとAg、CrとAuの組合わせによるナノストライプ構造を真空中で摩擦し、摩擦や摩耗が低下することを明らかにしています。また、マイクロパターン上にDLC(diamond like carbon、ダイヤモンドライクカーボン)を成膜し、摩擦や摩耗も低減効果を大きく異なる荷重条件で調べています。
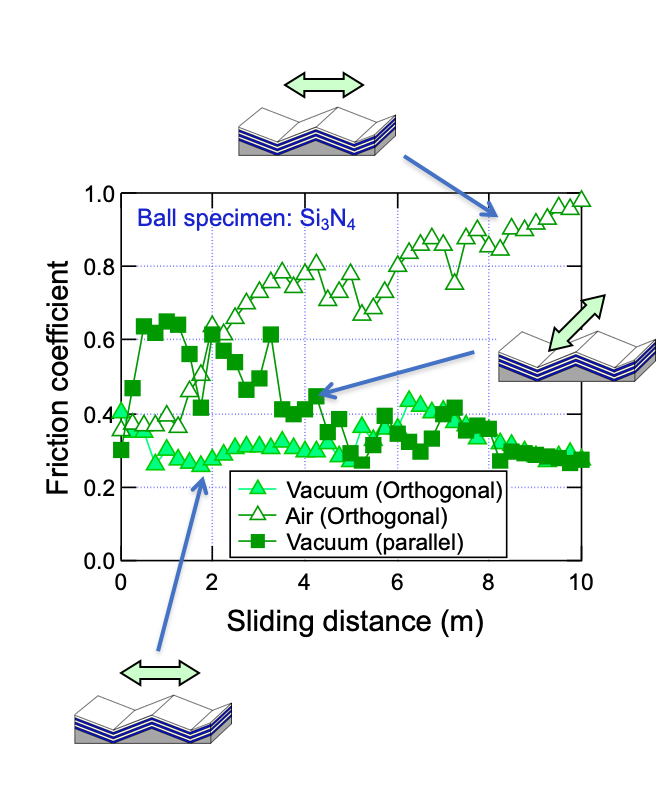
図1 真空中および大気中で、Ag-Crからなるナノストライプを摩擦したときの摩擦係数の変化。大気中では、Agが酸化するため低摩擦は発現しない。真空中で摩擦した場合、ナノストライプを構成する溝に対して直交方向に摩擦したときには、早い段階から0.25程度の摩擦係数を示す。それに対して、溝に対して平行方向に摩擦すると低摩擦を示すまでに多くの修道会数を必要とした。これは、直交方向に摩擦したときの方が、AgがCrの上に乗り上げやすく鳴るからである。
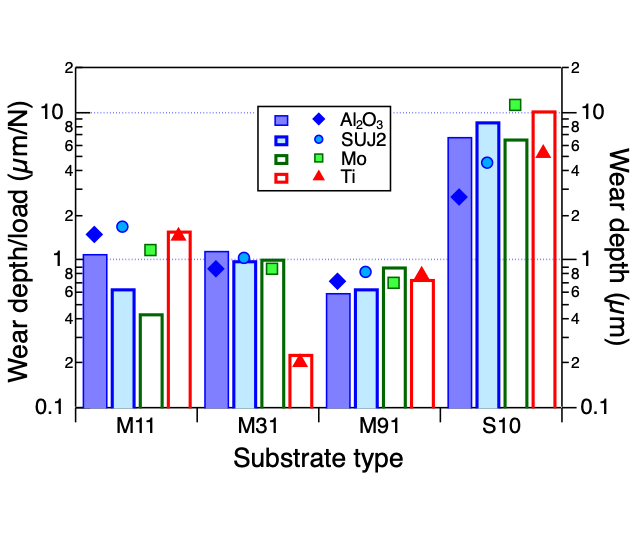
図2 異なる相手材料に対するナノストライプ構造の摩耗率の比較。M11〜M91はナノストライプ構造で、例えば、M31はCrとAgの膜厚比が3:1であることを示す。S10はCrの単層膜を示す。硬質材料のCrのみ(S10)よりも、Cr層の間にAg層挟まれた多層膜構造の方が、1/10程度低い摩耗率を示している。